Requirements:
Tunning of the advance curve, with engine speed, load and engine temperature compensation
Calibration on-the-fly (instantaneous), keeping it in memory
Use your own mobile phone as a calibration and monitoring
tool, to analyse the engine functionality (engine speed, advance applied and
etc), failure diagnosis, data recorder…
AC CDI (Use the energy generated by engine to do the spark
ignition)
Speed Engine Limiter
Low cost
Easy to install and configure
Software description:
The software concept is create a general plataform (RTOS),
basicly a temporal function scheduller with independent comunication (using
buffers for inputs and outputs), and a dedicated routine to handle the priority
ativities (specially ignition timing and comunication). Due
your modularised concept, it is possible to implement new
features on demand, the system are drive to interrupt.
I´m not use FreeRTOS or other operational system, in my
case, I developed my own OS (elementary) for this application, very simple but
powerfull and easy to maintain.
In my concept, I choosed to calculate in runtime the scenario
to applie the spark ignition (I use the n-1 data to predict n), different of
the most Microcontrolled CDI systems, that use table values to minimize the
microcontroller proccessing, the ARM Cortex M4 it is very powerfull for that...
There an specific order to treat all the information data
and event management, and priorize each one, that’s the secret to implement
succesfully this kind of system, I have a little experience for this.
Hardware
This is my Achilles' heel, I created a simple prototype
electronic board and I had many problems
with EMI and RFI, wich I can not eliminate.
For my luck, this kind of interference, it can be filtered
by my software strategy, even using opto-couplers, I could not eliminate all
existing noise.
The biggest challenger, it was to build all the electronic
structure: change HV coil, install sensors, create a wire harness, build circuits...
Start the project
The initial project is building a AC-CDI using some parts that exists in newest Walk Machine (CDI version).
Bellow I will show you how was old assembly and how the new part was it changed:
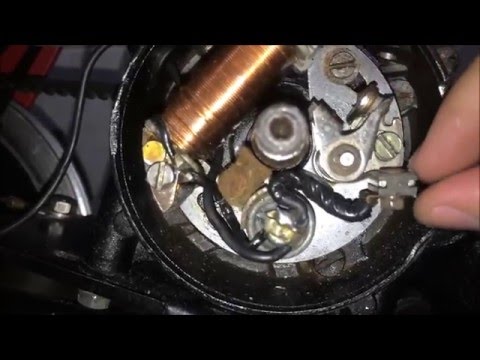
This picture above I found on internet, its not my engine, but is similar!
The new part:





High Voltage Coil, Its a ignition coil for Yamaha DT200
I created my own instrumentation system, Its very complex install sensors in this engine because it is very small, totally compact and optimazed...

Two hall sensor (I did not have two equal, I used one DN6851 as 20BTDC and one SS41 as 60BTDC, for hold in position a used cotton and super glue.


No comments:
Post a Comment